For Older Locomotives
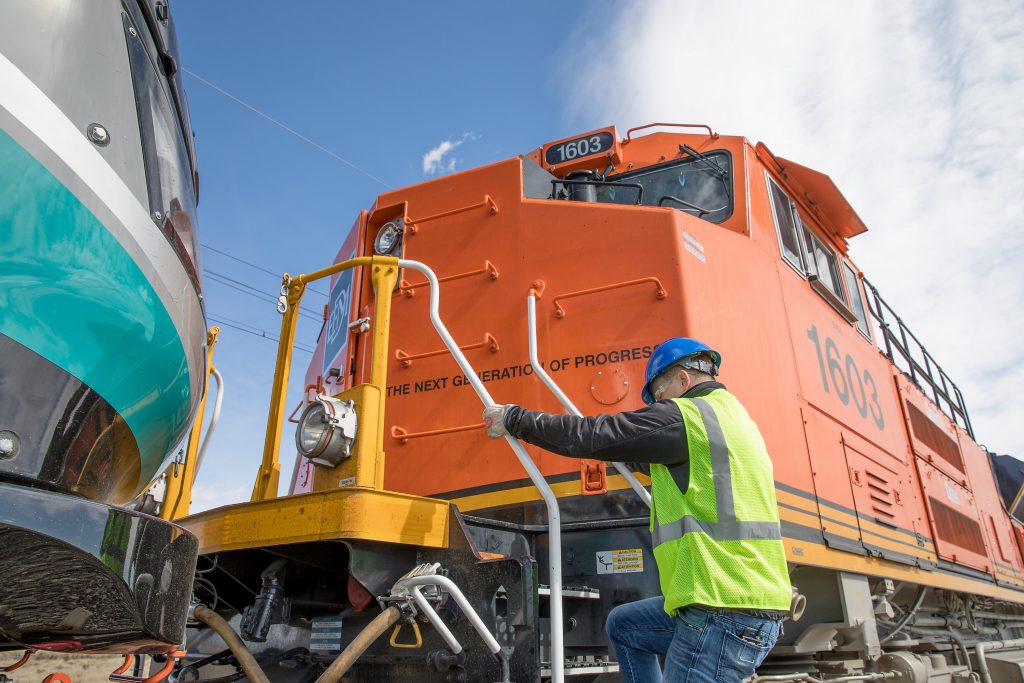
ABSTRACT:
Mitigating engine exhaust noise from older locomotives is a substantial challenge. The engine noise is broadband, but also includes prominent low-frequency tones that vary with engine speed. There is very little space inside the locomotive, so while a silencer would ideally be as large as possible, it must fit within tight constraints around other locomotive equipment. Many older locomotives have two-stroke engines that are highly sensitive to back pressure and were designed to run with direct ventilation to atmosphere. This imposes tight constraints on the flow resistance that a silencer can introduce, thereby constraining the design options.
This paper presents a successful case study in mitigating engine noise from an older locomotive. A team of Hushpak Engineering, UTS Tech Lab and Acoustic Studio designed, built and commissioned silencers for the C Class locomotives. The paper discusses how the design challenges of space, back-pressure and low-frequency tones were addressed. It also describes how developing the acoustic solution was not enough to deliver a suc- cessful project. The team had also to design and implement an upgraded crankcase ventilation system to maintain correct engine operation with the silencer in place.
This project showed that silencers for older locomotives can be efficient, effective and inexpensive, and highlights a way forward for addressing noise across the fleet of older locomotives that will remain in service for years to come.
Locomotive noise, after wheel squeal, is one of the main noise impacts on communities living near rail lines. This is particularly the case in Sydney which is surrounded by steep inclines where locomotives emit maximum noise levels for extended periods as they haul freight trains along the busy East Coast main lines.
Locomotives on Australia’s standard gauge network are diesel-electric, meaning they have a large diesel engine that drives an alternator which in turn drives electric traction motors to turn the wheels. The exhaust from the diesel engine is the dominant source of noise on these locomotives. The noise is broadband in nature, but includes substantial low-frequency tones (<100Hz) associated with engine firing. Locomotives have eight (8) engine “notches” in which they can operate (excluding idling). Engine speed, and hence the frequency of the tones, increases with engine notch.
This project involved designing an engine exhaust silencer for the C Class locomotives. The primary objective was to reduce low-frequency noise emissions to approximately the levels of modern locomotives. These are de- scribed in the Environment Protection Licenses of the rolling stock operators (NSW Environment Protection Authority, 2020).
1.1 C Class Locomotives
C Class locomotives were manufactured by Clyde Engineering in 1977/78. They are a 3000hp mainline locomo- tive powered by a turbocharged V16 EMD 645-E3 engine. Ten (10) C Class were built, and six (6) are in service with Southern Shorthaul Railroad (C504/5/6/7/9/10).
Locomotive such as C Class are incredibly durable. Even with 40+ years of active service, C Class is expected to remain operational in NSW for at least another decade. They play a key role in delivering low-margin freight services, particularly transporting agricultural produce to ports, which offer insufficient returns and longevity of haulage contracts to support the purchase of new locomotives. By remaining in service, C Class helps to keep hundreds of trucks off NSW’s roads, easing congestion and reducing greenhouse gas emissions.
C Class however, were among the loudest locomotives in mainline operation through Sydney. They were identi- fied by the community as being subjectively loud, particularly emitting high levels of low frequency noise.
2 - NOISE MITIGATION FOR OLDER LOCOMOTIVES
Older locomotives like the C Class were not designed to have silencers. This is particularly challenging for noise control because:
- There is very little space available on the locomotive to accommodate a silencer. The envelope of the locomotive is constrained by loading gauge restrictions imposed by tunnels, older bridges and overhead wiring. A silencer must therefore fit within this outline gauge, along with all the other equipment on the locomotive. In general terms however, the silencer should be as large as possible to improve its acoustic performance because:
The length of the chambers need to approximate the quarter wavelength of the low frequency diesel engine noise, in order to effectively mitigate this low-frequency. The dominant frequencies on C Class are between 30Hz and 100Hz, a wavelength range of between 6m and nearly 20m;
It can accommodate larger expansions in volume, and hence bigger impedance changes (which reflect acoustic energy within the silencer and therefore prevent it escaping as noise), without imposing re- stricter levels of back-pressure; and,
There is more space to accommodate acoustic absorptive material to mitigate high-frequency noise.
- The engine is very sensitive to back-pressure. This is particularly the case for EMD engines which are two-stroke1. This places substantial restrictions on the design of the silencer in order that the operation of the locomotive is not compromised. Excessive back-pressure can:
De-rate the engine, reducing the power that it can produce, and increase both fuel consumption and diesel emissions.
Cause the engine to shut down. Locomotives commonly have systems to protect the locomotive from excessive crankcase pressure. The crankcase on older locomotives is ventilated through the exhaust. Excessive back-pressure can lead to increases in crankcase pressure which trigger these protective systems to shut down the engine.